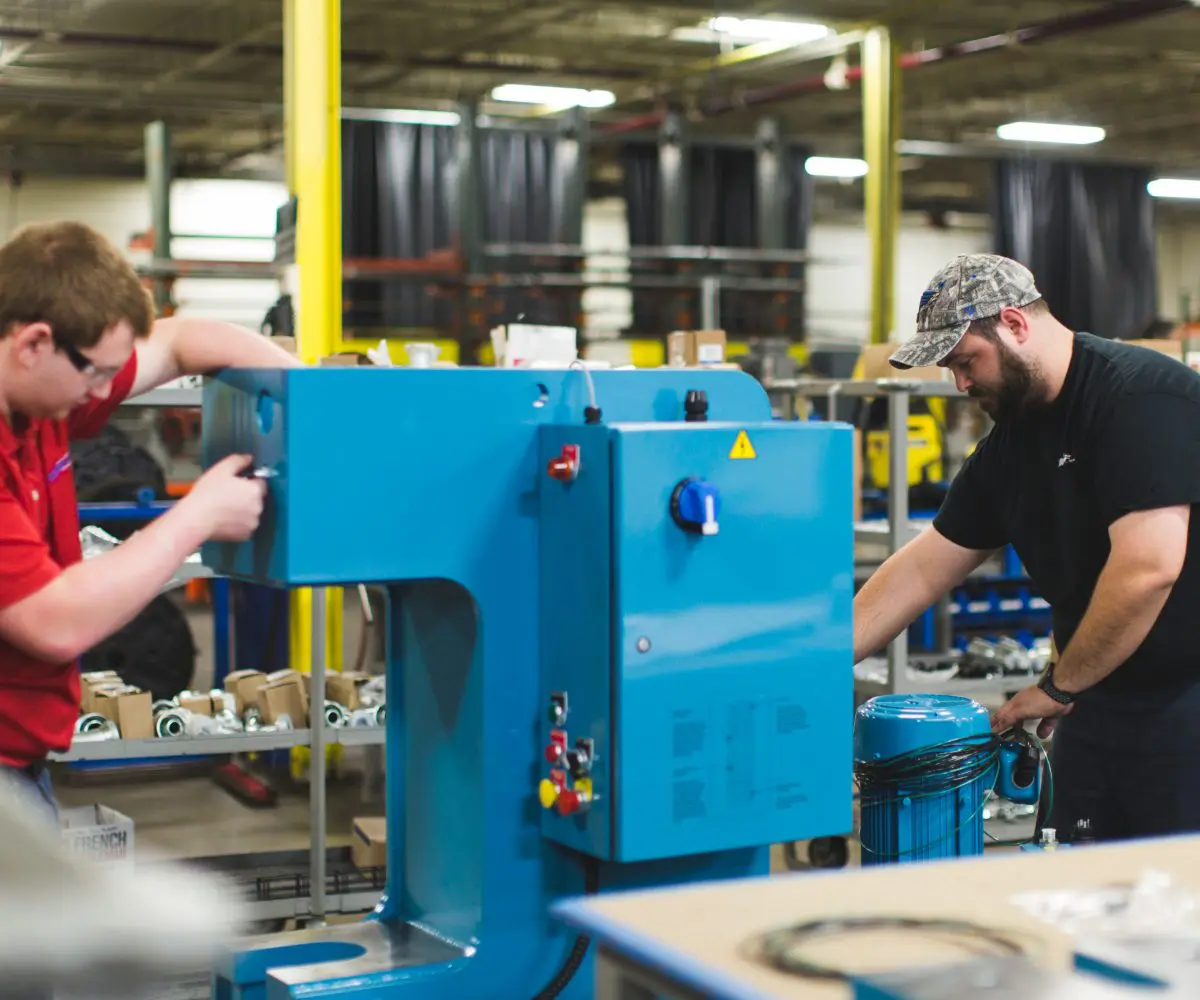
Engineering
Experienced and Dynamic
Our team of committed engineers comes from a diverse mechanical background, including machine design, project management, and automation experience. This is a team of people who love designing machinery and never stop innovating. A good press design begins with the basic building blocks of project management, mechanical, hydraulic and electrical design. Everything engineered at Neff Press is done in-house; we don’t outsource our designs. We can confidently say that our entire engineering team is well-versed in these areas, which results in high-quality press that will last a lifetime.
Project Management
Neff Press engineers are customer-focused.
A project engineer is assigned as the main point of contact and works with the customer from design through commissioning. Each customer gets the same treatment, no matter the size of the project.
This includes:
-
Reviewing the project scope and determining deliverables during an Engineering Kickoff Meeting.
-
Collaborating with our customers during the design process via online or in-person design reviews.
-
Helping the customer understand and update legacy processes. It is common that Neff Press Inc facilitates a better understanding of our customers’ in-house processes and highlights where improvements are applicable.
-
Compliance with a variety of customer-specific machine standards.
-
Managing process qualifications and runoffs on our floor (FAT) and acceptance at the customer’s factory (VAT).
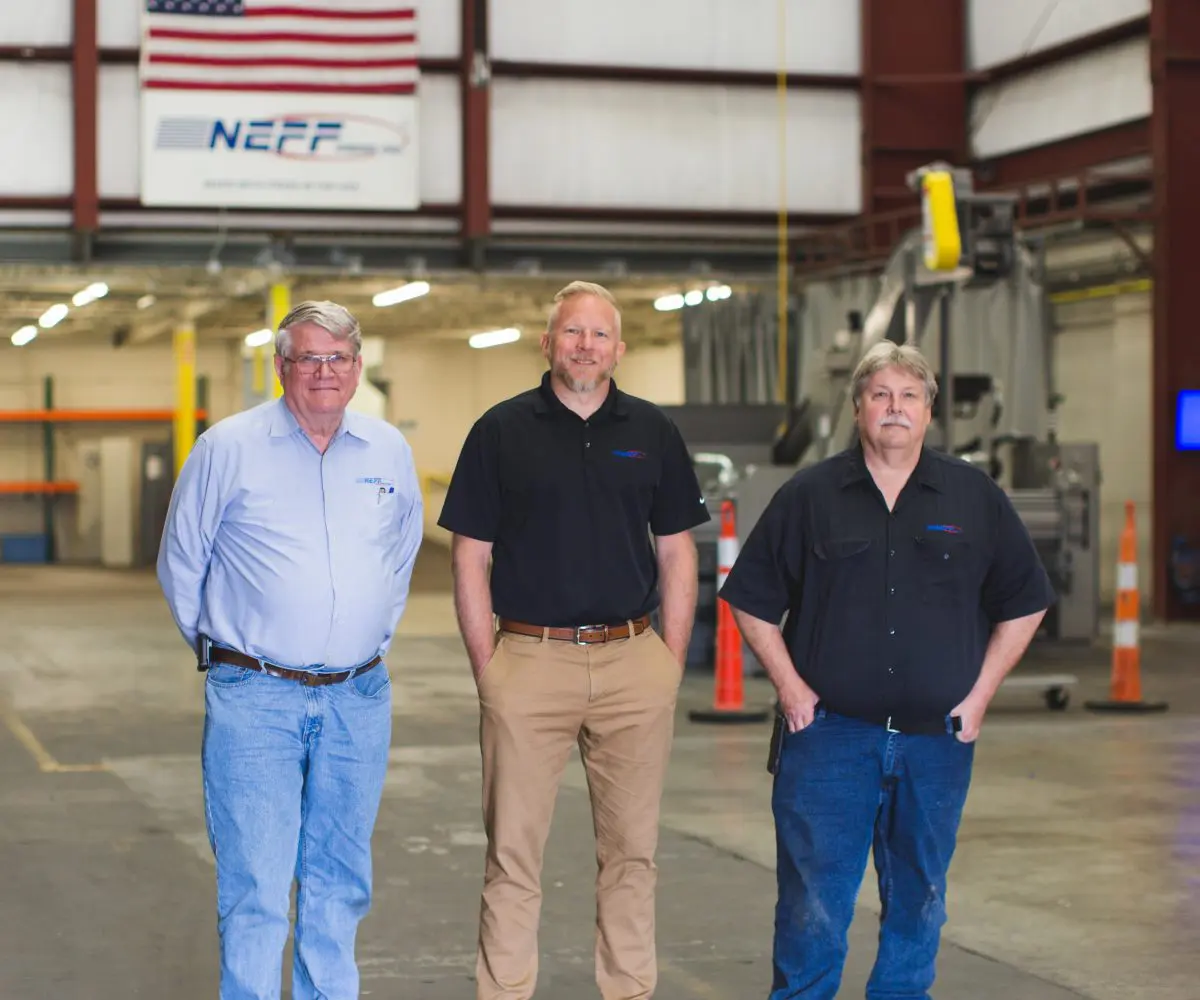
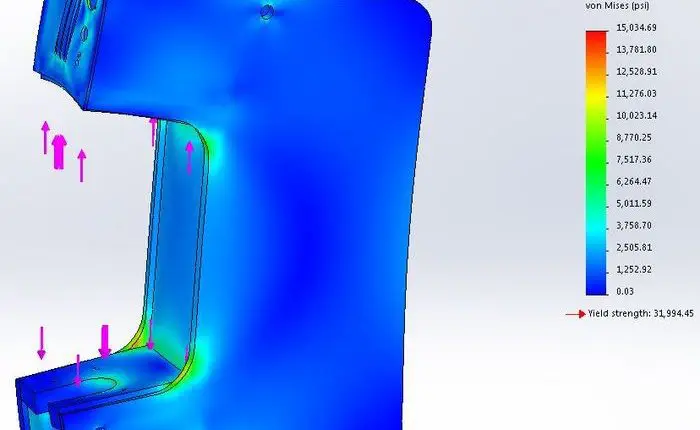
Mechanical Design
Advanced and Dependable.
-
Application experience to select the correct press frame based on loading conditions, tool clearance and other factors. Neff Press Inc’s engineering employs many proprietary press designs that ensure a dependable press.
-
Complex 3-D CAD modeling via SolidWorks Professional – Finite Element Analysis and Motion Simulation via SolidWorks Simulation Pro ensures a robust press frame.
-
Wide application experience in the selection of tool steels for all press applications.
-
Broad experience in a variety of mechanical technologies, including:
- Material handling devices like coil feeds, indexers, shuttles, robots and pick and place units.
- Rack and pinon variable-speed multi-axis drives for gantry machines and Drive-by-Wire joystick control
- Quick die change and die racking equipment.
- Heated and chilled platens and process chillers.
- Downstream inspection via scales, vision, and contact and non-contact probes.
- Augers, gearboxes, and roller chain.
-
Integrate robotic and automated solutions to increase output, precision, speed, and safety.
-
Ability to collaborate with customer part and die files via a variety of 3-D file formats.
-
Simulation of complicated machine installations and rigging by mimicking the customer’s factory in a 3-D environment.
-
Continuous improvement and advancement in robotics, and industrial automation technologies maximizes our customers productivity.
HYDRAULIC DESIGN
Clean and Robust.
-
Scalable designs are as simple as discrete valving up to precision servo hydraulics.
-
Clean design using proprietary integrated manifold blocks with test ports for troubleshooting.
-
Energy-efficient hydraulic units through load-holding check circuits, accumulators, and variable-speed pump drives.
-
Hydraulic units are built on fundamental principles such as:
- Special attention to fluid velocity, tank size, tank layout, pump suction condition, and control of fluid aeration.
- Fluid condition management, including filtration, particle counters, cooling and sealed systems.
- Redundant valving for safety compliance.
- High safety factors on pressure-rated components.
- Optimal motor selection via RMS sizing.
-
Capability to use fire-resistant and ecologically safe hydraulic oils (Water-Glycol, Quintolubric, EcoSafe, etc.).
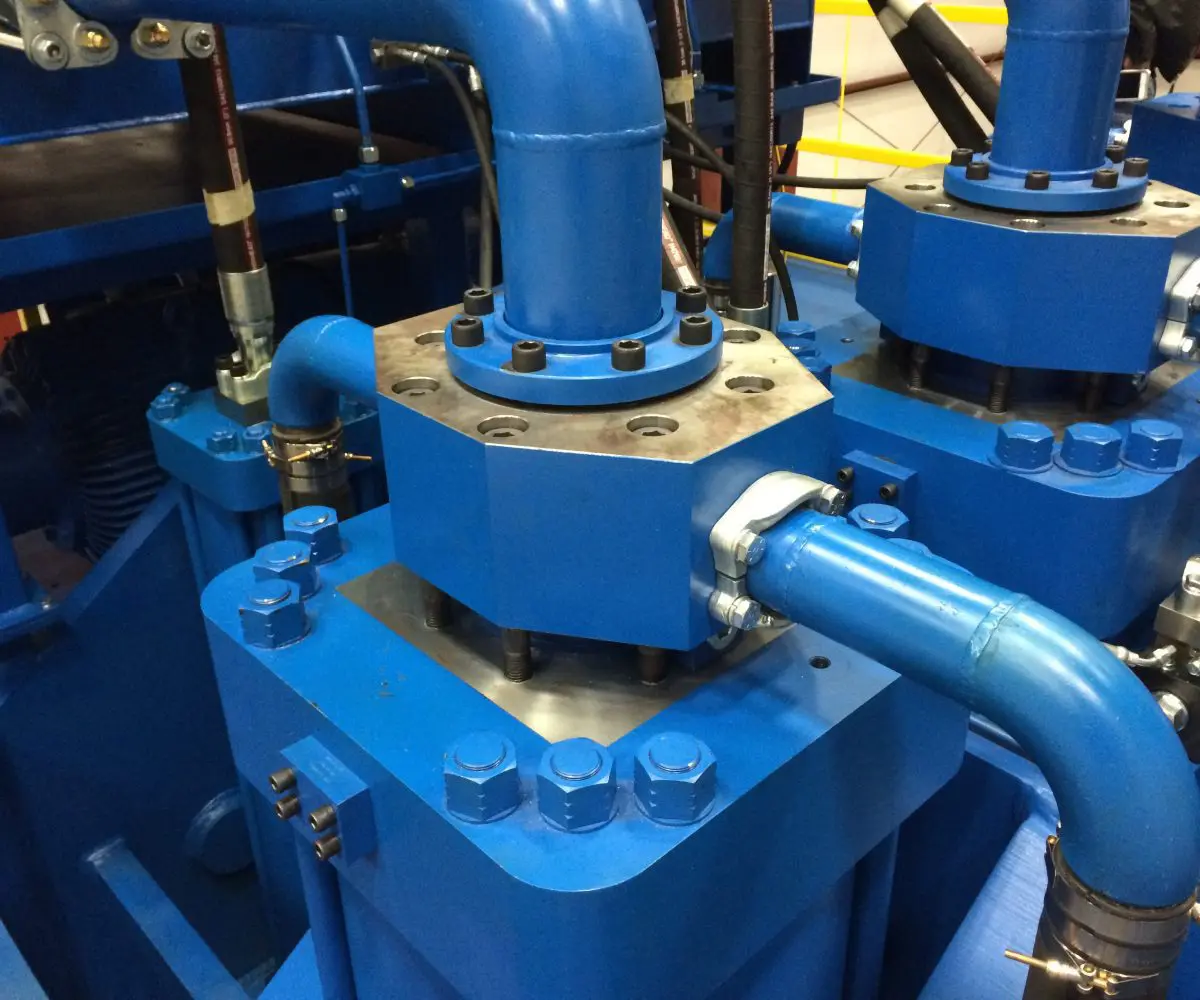
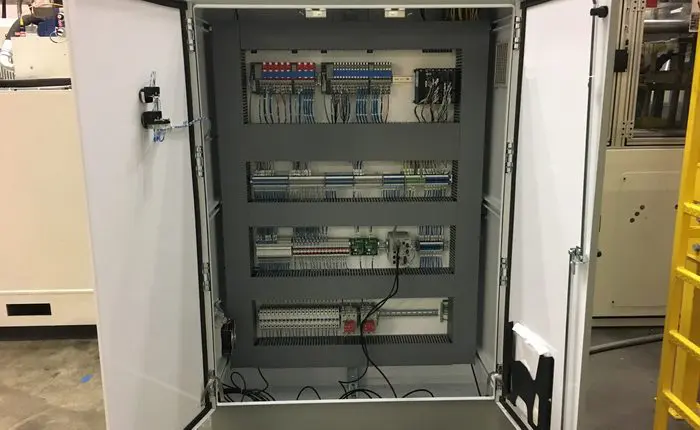
ELECTRICAL DESIGN
Safe and Modern.
-
Sound “by the book” electrical design with UL 508a certification, NFPA 70 and NFPA 79 compliance.
-
Safety code Compliance ANSI B11.2 (1995), CSA Z142, and EN693, as well as pertinent OSHA standards. A Neff Press engineer sits on the board of the ANSI B11.2 committee. When necessary, Neff Press Inc works with the approving entity (ex: Pre-start contractor for CSA Z142) to ensure expedited sign-off by the third-party inspector.
-
Explosion-proof designs comply with NEC 505 and ATEX.
-
Expertise with widely accepted and modern software, such as:
- PLC Programming – Allen Bradley (Rockwell Toolkit), Siemens (TIA Portal), etc.
- Delta RMC Tools
- Schematic design and panel layout using AutoCAD Electrical
-
Safety controls range from as simple as a safety relay to full-blown safety PLC solutions.
-
Process reporting (OEE, pass/fail data, press-fit curves, in-die quality analysis, and diagnostics).